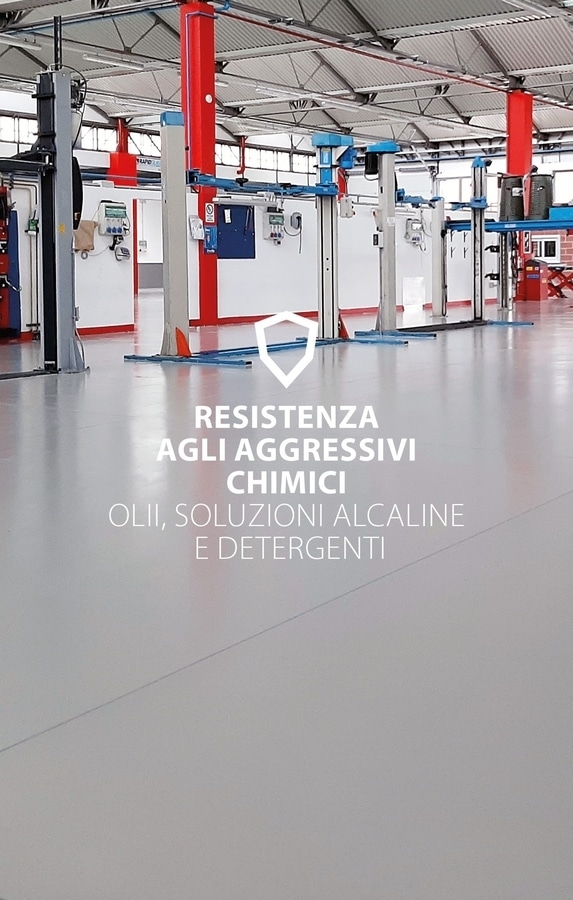
Voir la traduction automatique
Ceci est une traduction automatique. Pour voir le texte original en anglais cliquez ici
#Actualités du secteur
Résine autonivelante pour sols industriels
La meilleure résine pour l'industrie
Qu'est-ce que la résine autonivelante ?
La résine autonivelante, généralement époxy, est un type particulier de résine capable de s'autoniveler sur des surfaces horizontales préparées avec un apprêt et déjà soumises à un cycle de traitement. Elle est obtenue par la combinaison d'une résine et d'un durcisseur, mélangés ensemble. Le mélange obtenu peut être appliqué sur des supports en bois, en ciment et en carrelage pour créer une surface solide et durable.
Une fois durcie, la résine autonivelante a un aspect brillant, elle est imperméable et résistante à l'abrasion. Ses propriétés chimiques et mécaniques restent inchangées sur toute son épaisseur, qui est généralement de 2 à 3 millimètres.
Les résines autolissantes conviennent à de nombreux environnements exigeant une excellente hygiène et des lavages fréquents ; par exemple, elles sont souvent utilisées dans les industries mécaniques, alimentaires, chimiques et pharmaceutiques, les laboratoires et les hôpitaux. Elles sont également souvent choisies pour l'uniformité et la régularité de la surface finale.
Un type particulier de résines autonivelantes sont les résines transparentes, qui permettent d'incorporer divers objets, en créant des effets originaux et agréables. Dans ce cas, l'épaisseur peut atteindre plusieurs centimètres.
Comment doit être le support ? Peut-il également être irrégulier, puisque la résine est capable de s'auto-niveler ?
En ce qui concerne le support, il peut également présenter de petites irrégularités ou être endommagé superficiellement, car l'épaisseur créée par le cycle d'application (primaire + taloche) est en mesure d'égaliser la surface.
Attention toutefois : le support doit dans tous les cas être exempt d'irrégularités importantes qui ne pourraient pas être comblées par un matériau de 2 à 3 millimètres d'épaisseur.
En cas de différences de niveau importantes, un mortier époxy peut être appliqué au préalable afin de créer une surface uniforme sur laquelle la résine autonivelante peut être appliquée.
Quels sont les avantages de la résine autolissante ?
Les sols en résine autonivelante sont très populaires dans les secteurs commercial et industriel.
Ceci pour de nombreuses raisons, brièvement décrites ci-dessous :
Surface lisse et plane
La planéité caractéristique offerte par la résine autonivelante, associée à la résistance aux charges, est une garantie supplémentaire de sécurité dans les environnements où passent fréquemment des chariots élévateurs ou des élévateurs à fourche, transportant souvent de lourdes charges. L'absence d'échappées, typiques des carreaux, et la présence limitée de joints, rendent la surface facile à nettoyer et limitent considérablement l'accumulation de saletés et de bactéries.
Faible épaisseur
Comme nous l'avons dit, l'épaisseur est de l'ordre de 2,5 à 3 millimètres : suffisamment réduite pour ne pas avoir à modifier les aménagements, surtout en cas de rénovation.
Une robustesse remarquable
Les sols autolissants en résine ne subissent pas d'altérations suite aux lavages fréquents, aux agents chimiques, au passage continu de personnes et de véhicules. Cela permet une installation dans des environnements aux exigences très spécifiques, tels que les industries alimentaires, les industries pharmaceutiques, les hôpitaux ou les laboratoires.
Élasticité
Les résines autolissantes ont un bon degré d'élasticité, ce qui les rend également adaptées à la pose sur des sols présentant de petites irrégularités de surface.
Temps réduits
Les temps de pose et de durcissement réduits caractéristiques des sols en résine sont également maintenus par les résines autonivelantes : cela permet de minimiser les temps d'arrêt de l'activité de travail.
Rendement esthétique élevé
La surface est esthétique : généralement opaque, elle peut être rendue brillante, avec un aspect "vitreux" ; les joints, malgré les joints classiques, sont peu visibles et rendent la surface presque linéaire et uniforme : même dans les environnements industriels et commerciaux, l'œil veut sa part !
Personnalisation
Bien qu'elle ait généralement un aspect lisse et vitreux, la résine autolissante peut être rendue antidérapante par l'application de finitions spécifiques, par exemple pour rendre la surface rugueuse et générer précisément des zones antidérapantes. En outre, comme d'autres applications typiques de la résine, le cycle autolissant permet également de nombreuses possibilités de personnalisation, aussi bien, par exemple, avec l'insertion d'écritures, aussi bien en termes de couleurs qu'avec la création de signes horizontaux ou d'autres spécifications.
Dans quels environnements la résine autonivelante peut-elle être appliquée ?
Grâce à sa polyvalence et aux nombreux avantages qu'elle offre, la résine autonivelante peut être utilisée pour diverses applications industrielles et commerciales.
Par exemple, des réalités telles que les showrooms et les magasins peuvent profiter de la finition brillante et des nombreuses possibilités de personnalisation capables de rendre chaque environnement unique et donc personnalisable.
La surface uniforme, résistante aux chocs et à l'abrasion, est idéale pour les entrepôts et les dépôts, où les chariots élévateurs circulent tous les jours. Ces mêmes caractéristiques font des sols en résine autolissants un choix pratique pour les entreprises manufacturières également.
Grâce à l'absence de voies d'évacuation et à la possibilité relativement élevée de nettoyage et d'assainissement, les résines autolissantes peuvent également être posées dans les hôpitaux, les laboratoires et les environnements où des aliments sont préparés (par exemple, les cuisines industrielles, les restaurants, les entreprises alimentaires).
La résistance à l'huile, au carburant et à d'autres produits chimiques permet une application à l'intérieur des garages et des ateliers.
Comment poser la résine autolissante ?
Quel que soit le type de cycle d'application, à chaque fois que l'on crée un sol en résine, il est important de s'assurer que le support est propre et qu'il n'est pas contaminé par de la graisse, de l'huile ou de la poussière, ce qui pourrait compromettre le résultat final.
En ce qui concerne les résines autolissantes, après une préparation mécanique soignée et une couche d'apprêt sur le support, la résine est généralement versée, puis étalée à l'aide d'une truelle dentelée, afin d'obtenir un résultat uniforme. Immédiatement après l'étalement à l'aide d'une spatule, l'installateur passe le rouleau brise-bulles pour éliminer l'air emprisonné pendant la phase de mélange.
Sivit propose différents cycles d'auto-nivellement pour de nombreuses applications et pour des supports dans des conditions variées.
Dans ce paragraphe, nous décrivons les phases d'application des cycles d'auto-nivellement époxy et d'auto-nivellement transpirant ; pour toutes les autres solutions, visitez la page " Auto-nivellement ".
Cycle d'auto-nivellement époxy Sivit
Pour les supports en béton sans problèmes particuliers, nous proposons le cycle d'autolissage époxy, à base de résines époxy et sans solvants.
Si la base en béton (béton) vient d'être achevée, il faut attendre le temps de durcissement normal (généralement environ 30 jours) avant de poser la résine autonivelante. Dans tous les cas, le support doit être solide, sec, plat et exempt de toute contamination par des huiles, des détergents, des poudres ou d'autres substances.
Avant de commencer les travaux, procéder à la préparation mécanique du support par sablage ou grenaillage afin de garantir une bonne adhérence des produits.
Le cycle d'auto-nivellement de l'époxy se compose de quatre phases.
Première phase
Après avoir préparé le support, on applique une couche de Fluidepox, une formulation époxydique transparente sans solvant chargée de quartz sphérique enrobé de résine, en guise de skim coat.
Pendant que le produit lui-même (Fluidepox) est encore frais, du quartz est saupoudré sur la surface.
Deuxième phase
Le mortier est préparé en combinant les deux composants de Paviplast, une formulation époxy colorée et sans solvant, autolissante et chargée de quartz. Le mortier autolissant est coulé, le produit est réparti à l'aide de la racle dentée et la surface est uniformisée à l'aide d'un rouleau brise-bulles.
Troisième étape
En fonction de l'environnement visé, il peut être souhaitable d'atténuer la brillance de la surface et de la rendre légèrement rugueuse.
Dans ce cas, on peut appliquer au rouleau une couche de Paviwater colorée, diluée à 10% avec de l'eau, additionnée de microsphères de verre pour obtenir des surfaces antidérapantes.
Quatrième étape
Le revêtement est découpé au niveau des joints de béton et scellé avec Sigilflex, un produit élastique et résistant.
L'épaisseur finale du revêtement est d'environ 2,5 à 3 mm.
Cycle auto-nivelant Sivit transpirant
Les fonds présentant des remontées d'humidité nécessitent un traitement spécifique afin que la couche de résine ne soit pas endommagée au fil du temps. En effet, l'humidité peut provoquer la formation de condensation, de bulles d'air, voire forcer le décollement de la résine du support.
Sivit a donc mis au point un cycle d'auto-nivellement transpirant destiné à ces types de supports, dont la mise en œuvre se déroule en cinq phases :
Première phase
Une couche d'Ecofondo dilué à 15% avec de l'eau est étalée au rouleau sur le support convenablement préparé. Il s'agit d'un produit qui crée une barrière à l'humidité et qui est donc utilisé comme couche de fond pour les surfaces humides.
Deuxième phase
Une deuxième couche d'Ecofondo est appliquée, diluée à 10 % avec de l'eau et additionnée de 10 % de quartz.
Troisième phase
Application au rouleau de deux couches de Paviwater T68, chacune diluée dans l'eau.
Quatrième étape
Il est coulé et réparti avec la lame dentée Paviplast W, une formulation époxy colorée.
La surface est ensuite passée au rouleau brise-bulles pour créer une couche uniforme.
Cinquième étape
Le revêtement est découpé au niveau des joints de béton et scellé avec Sigilflex, un produit élastique et résistant.
Une fois le travail terminé, l'épaisseur finale sera d'environ 2 mm.
Voici une vidéo dans laquelle nous montrons pas à pas la création du cycle auto-nivelant respirant : https://youtu.be/GgplyByYmnQ